Clean Sky 2 – Innovative Physical Integration Cabin とMFFDに関してのメモ
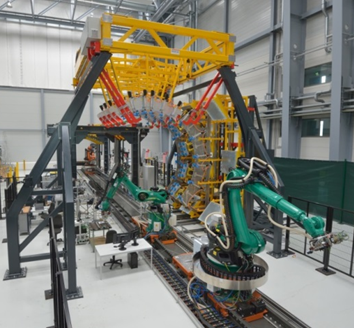
Multifunctional Fuselage, Cabin and Systems Integration Image: Clean Sky website
Clean Sky 2は、航空機の騒音、排出ガス、二酸化炭素排出量を削減する技術開発のための欧州パートナーシップです。高効率な翼、軽量で高効率なエンジン、新しい航空機の設計・構成、よりスマートなシステムとすべての分野を見直してそれらを達成しようというプロジェクトです。このプロジェクトでは複合材がその材料として目立っていますが、金属も開発されています。
1980年代後半から同様の研究が行われ、多くの研究が技術成熟度レベル(TRL)6まで行われ、実証モデルでの研究まで行われてきました。研究の成果は実際の機体にも採用されており、エアバスA350でも採用されています。
今回のClean Sky 2の1つに「Large Passenger Aircraft」があり、大きく:
Platform1 – 先進的エンジンと機体構成
Platform2 – 胴体と客室への先進的技術の研究
Platform3 – 次世代機体・コックピットシステムと電子機器
の様な感じで別れています。(詳しくはClean Sky2のサイトをご覧ください。)
今回メモしておきたいのは、それぞれのPlatformで製造する実証用のモデル(Innovative Aircraft Demonstrator Platform (IADP))ですが、フルスケールで製造されます。特にPlatform2はWP1.1で「Next generation fuselage, cabin and systems integration」とあり、ここでMFFD – Multifunctional Fuselage Demonstratorという実機サイズの胴体セクションで製造予定です。
MFFDの目指すところ:(読んだ感じ。)
● 熱可塑性CFRPを使用した胴体構造、客室、貨物室、システムの実証
● 次世代のキャビンと組み合わせた革新的な設計原理と高度なシステムアーキテクチャ
● 月産70-100機の大型旅客機の生産率を実現
● Recurring Cost(RC:リカリング・コスト)を削減し(20%)、胴体重量を1トン削減
● システム軽量化とシステムアーキテクチャ統合の改善により、航空機全体のエネルギー消費を大幅に削減 = 燃料燃焼の大幅な削減、ひいてはCO2およびNOxフットプリントの削減
● 製造と自動化の設計、センサー化、データ分析など、インダストリー4.0を活用し望ましい製造コスト効果を実証する
● 製造プロセスの最適化により、製造時間の短縮=省エネルギー、高効率化でのCO2およびNOxフットプリントの削減
● 熱可塑樹脂複合材料の適用により、機体が運用終了後のリサイクル利用
製造される実証胴体に関してハーフ・バレル・デザインで胴体径:〜4m、セクション長:〜8m程となる様で、A320の胴体に非常に近いですが、円ではなく、卵の様な少し縦長の形状となる様です。
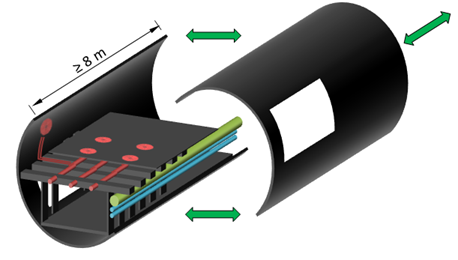
Multifunctional Fuselage, Cabin and Systems Integration Image: Clean Sky website
上記の目標を達成する上で鍵となるのが、Dustless Joining(ダストレス結合)で穴あけ作業による削りカスなどが無くなるという意味ですが、孔無し、ファスナー無しを目指し、熱可塑複合材の融着(welding – 溶接)による接合が採用されます。現在行っているのは、融着を使用した大型の熱可塑性樹脂構造の接合の調査とテスト段階です。熱可塑性樹脂は、構造物やその接続ブラケットとアンカーポイントに現在使用されているものよりも高価な材料ですが、自動化して効率を上げることができるため、全体的な製造コストを削減できるとみています。
機体組み立てのコンセプトも面白いもので、通常だと機体の構造が組み立て終わってから客室や貨物室を仕上げて行きますが、このプロセスが機体製造する上で時間がかかる部分と見たようです。これを解決する為にMFFDでは予め機体構造に装備品を取り付けたモジュラー構造体を組み上げることでその時間短縮を目指しているようです。
これが実現できれば、航空機のオペレーターにとってモジュラー形式の設計により、航空会社が新しい座席、キャビンの仕切り、ギャレーなど客室内のアイテムを変更したい場合、今よりも容易にインテリアを調整および変更できます。機体で共通の熱可塑性樹脂製のアンカーポイントを備えたコンポーネントを設計することで、将来の客室内装の変更をより簡単に実現できると考えています。
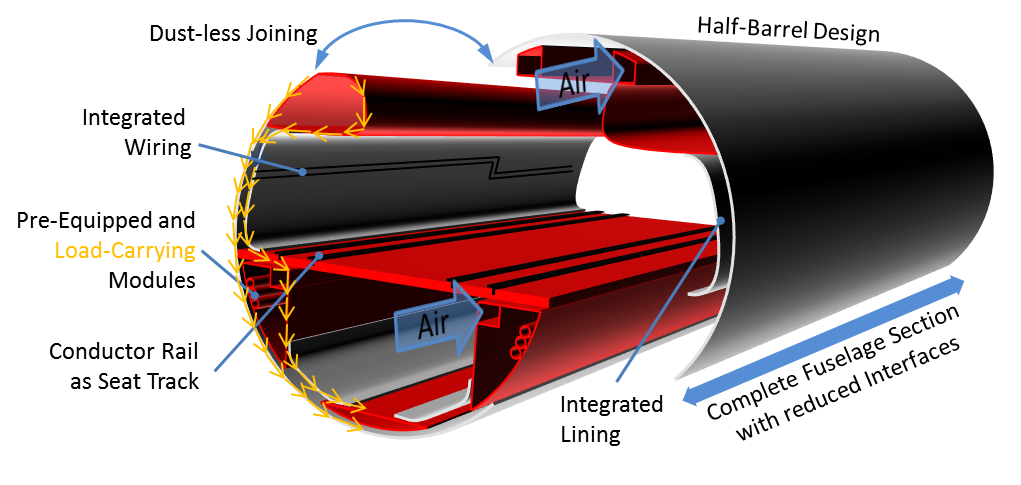
Multifunctional Fuselage, Cabin and Systems Integration Image: Clean Sky website
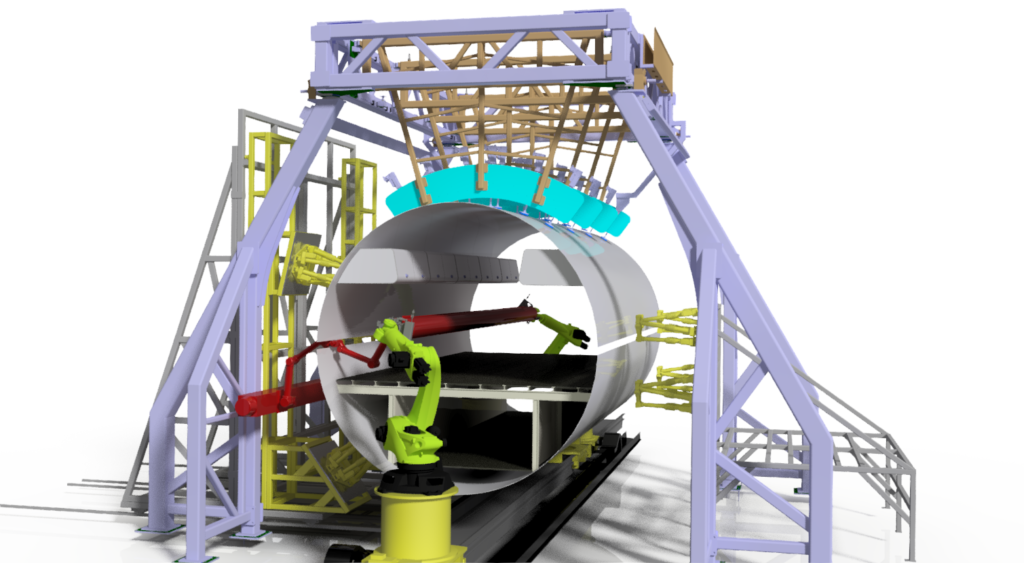
The Next Generation Multifunctional Fuselage, Cabin and Systems Integration Image: Clean Sky website
計画では、2020年に実際の胴体バレルの生産を開始し、2022年末までに完成させる予定です。
このMFFDの中でもいくつかのプロジェクトに分かれていますが、そのなかでSTUNNING(STUNNING (SmarT mUlti-fuNctionNal and INtegrated thermoplastic fuselaGe))とMECATESTERS (Micro mEchanical Characterization of A ThErmoplastic Co-conSolidated/welded joinT for usE in aiRcraft fuSelages)があります。
STUNNING:
MFFDで全て装備が取り付けられた胴体下半分を開発するプロジェクトで、参画しているメーカーは:
GKN Fokker:同社の4部門が参加しています。Aerostructures (オランダ・パーペンドレヒト)、Fokker ELMO (オランダ・ホーヘルハイデ)、GKN Fokker Engineering Romania (ルーマニア・ブカレスト)、GKN Fokker Technologies (オランダ・パーペンドレヒト)です。Fokker ELMOでは電装ハーネスを担当し、同プロジェクトへの先進的電装システム・電源バスシステムを提案します。
Diehl Aviation:(ドイツ・ラウプハイム)サブシステムや客室フロア、サイド・ウォール・パネルの新たな接合方法などを含んだ内装品を担当します。
NLR :(オランダ航空宇宙研究所・アムステルダム)胴体スキン、ストリンガーを担当します。これにはTU Delftの超音波溶接技術の技術協力があります。
MECATESTERS:
これは大規模な溶接技術のテストプログラムです。 KVE Composites (オランダ・ハーグ)とRescoll (フランス・ペサック) が2019年4月から30カ月間にわたって調査研究を行っていきます。KVE社はファブリックとUDテープの両方における熱可塑性複合材料のインダクション融着の長い歴史があり、これまでファブリックの融着が採用された部品が航空機部品として使用されています。MFFDの研究の中で上記以外のレジスタンス融着と超音波融着に関しての調査も行いますが、STUNNINGプロジェクトでは、UD材とLM PAEK材料を使用した際の最適条件を探り、一般的な使用負荷と環境条件でのインダクション融着とコンダクション融着の比較を行う予定です。
これらが完了した後(2021年末頃)、胴体下面部分のMFFDはドイツ・シュターデのFraunhofer Institute for Manufacturing Techanology and Advanced Materials IFAMへ送られ、胴体上半分と結合されます。
MFFDプログラムの進行状況ですが、ホームページによると、2019年11月にCDR(Critical Design Review)を済ませており、2020-2021年にかけて”Digital Twin Phase”というフェーズに入っている様です。これはCDRでデザインはある程度確定してはいるものの、それぞれ部位のNDTデータやプロセスデータから得られたデータを設計データへフィードバックし変更を加える作業が行われています。これにより実際に製造されている製品に合わせた設計データに変更されます。2020年はこれらの部品を製造組立する年となります。
Clean Skyのプログラムを全てカバーするのは個人的に無理なので、今回はその中の一部。Dustless Joining(ダストレス結合)を適用した熱可塑樹脂コンポーネントを機体の主要構造部位に採用した次世代大型旅客機を、月産レート70機以上達成することを目標…いろいろやってるんだなとメモまで。
研究機関でシコシコと終わるだけでなく、実証機体→生産への適用というサイクルがある環境は良いですね。
参照リンク:
https://www.cleansky.eu/